Event seven for members of the Poultry Industry Programme was the held in the north of England. Being a free-range egg producer I was personally very excited to learn more about this area of the poultry industry.
Hearing the ins and outs of feed mills
We started the day at ABN’s Flixborough mill for a presentation on compound feed production and nutrition, followed by a tour of the site. First we were met by Danny Johnson, General Manager for ABN, who gave us an introduction to the business. ABN is a division of AB Agri, who employ over 700 people, supplying compound pig and chicken feed from 11 mill sites across the UK.
Brian Kenyon, Senior Nutrition Manager for ABN explained the factors which impact upon feed and nutrition; the environment, policies, and supply chain to name just a few. Then we met Ian Whittaker, the mill Operations Manager, who made a very interesting point about how adding new raw materials into a diet isn’t as easy as it sounds.
In order to add new materials into the diet rations, the mill needs to ensure that it has the space available to store the new ingredients and the facilities to handle the raw materials. They can then confirm a consistent supply of high-quality raw materials at an accredited standard for the UK poultry industry.
We were then shown around the mill. The Flixborough site specialises in the production of broiler feed. This enables them to efficiently manufacture large quantities of feed as they have fewer rations and raw materials, enabling a more streamlined process. We were able to see raw materials being delivered, right through to feed being loaded into the lorries ready for delivery to the poultry farms. It was a very clean, tidy and well-kept mill.
Experiencing a processing plant in action
In the afternoon we visited the 2 Sisters Food Group’s Foxhills processing plant and met Group Agricultural Manager Andrew Gibson, who was very good at describing the different processes and answering our questions.
Here, live chickens get delivered into the factory, and three and a half hours later chicken packed and labelled ready for the shops leaves the factory. It was an amazing experience to see the whole process from start to finish.
We were met by Head of Operations Dan Whillock, who gave us an overview of the business. He explained how the business has suffered from Brexit because of staff shortages and how they have changed to a five-day working week.
He also explained how they have changed their killing process to five stage gassing, which is better for bird welfare and the overall quality of the product.
It was also interesting to hear that the retail market has also changed from a large whole chicken to a smaller chicken.
At the 2 Sisters site they process eight birds a second, 480 every minute which equates to 2.5 million birds a week, sending five million kilograms of chicken out of the factory each week!
The tour around the factory showed us how technology and automation has helped their business strengthen and become a key part of the supply chain.
On behalf of the NFU and the PIP I would like to thank everyone at the ABN Flixborough and 2 Sisters Foxhills sites for the opportunity to visit and learn about your businesses.
More accounts from our 22/23 PIP cohort:
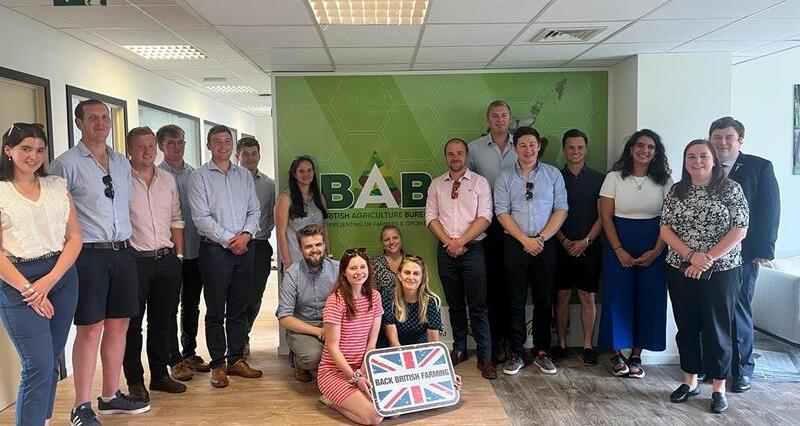