One of the easiest ways of keeping yourself safe is by ensuring all the equipment you require is properly maintained and therefore suitable for the intended tasks. This can apply to any piece of equipment you run, for instance tractors, trailers, ATVs, towed appliances, farm vehicles, handheld machines etc.
Not only will regular maintenance keep the machines and vehicles safe and efficient, it will also ensure they are compliant with the PUWER (Provision and Use of Work Equipment Regulations) legislation.
Daily and regular checks
By completing daily checks before commencing use of the machine or vehicle, you are more likely to notice any possible defects that could prevent the task being carried out safely.
In addition to this, regular maintenance checks completed by a dealership are also recommended to ensure any defects that are not highlighted on daily checks are addressed. This can ensure that small issues are repaired before they escalate and have a bigger financial and safety impact.
Maintenance. Why you should care.
It is important to ensure that equipment is maintained, and in good and efficient working order. ‘Efficiency’ of the equipment does not relate to productivity, but to the health and safety aspects of all parts of the machinery, however, keeping the equipment well maintained is likely to mean it will be more cost effective to run.
Employers must ensure that PTO guards, brakes, and hydraulic hoses are maintained and safe to use at all times. Employers must check equipment regularly to ensure that it has not deteriorated and become a risk.
The frequency of checks is dependent on the equipment itself and the risk involved; it could be each day, every three months, or even longer. Only those who are experienced and competent with the appropriate level of training should carry out maintenance work.
All equipment should undergo regular maintenance checks in accordance with the recommendations from the manufacturer. Where machinery has a maintenance log it should be kept up to date. The PUWER regulations do not require farmers to keep a maintenance logbook, but it is helpful to do so for reasons other than health and safety, such as evidencing of regular maintenance if the machine is ever hired or sold. The logbook should provide information for future maintenance planning and inform maintenance personnel and others of previous action taken.
A well-maintained vehicle or machine is more likely to be complaint with what is considered roadworthy. As such, if an incident should occur (that is not your fault), you are likely to be in a more favourable position if your vehicle or machine is well maintained.
For further guidance and examples of vehicle health checks, visit: Code of Practice: Vehicle Health Check Scheme
What does the law say?
Under the PUWER, if a defect occurs that is of significant risk to the operator, once the defect has been repaired, it must be subjected to a formal inspection to ensure the machine is suitable for use.
This inspection must be carried out by a competent person. Any inspection made under this regulation must be recorded and results retained until the next inspection takes place and this record must accompany the machine when borrowed/hired.
Examples of safety critical items which may need regular inspection include PTO guards, chain saw guards, tractor cab condition, a roll bar damaged in an accident and the parking brake.
PTO guidance
An example of equipment that should be regularly maintained and replaced when damaged are PTO shaft covers.
Some designs of PTO shaft covers make it harder to grease points on the PTO shafts. If possible, replace this type of cover with one that is more practical to manage.
The potential risk associated with a missing or damaged PTO cover is high and can result in a life-changing or fatal injury. Therefore, a missing or damaged cover should be replaced as soon as possible, and the PTO should not be used until an appropriate cover is fitted.
Covers should be fitted by an appropriately trained person, and should not be loose around the shaft, but fit snugly to minimise any movement of the cover around the shaft.
Further information on safe use and maintenance of agricultural machinery, review the HSE guide.
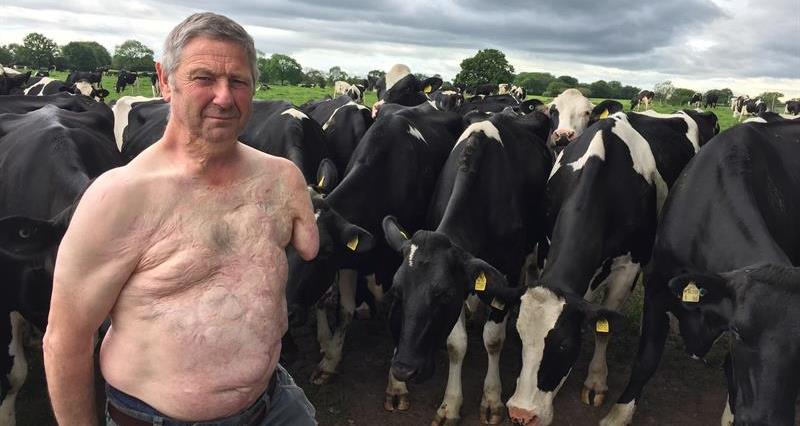
Testing
A good way of showing your machines are suitable for use is by getting them tested by competent persons. An example of this is brake testing. Trailer brakes are a wearing part and need adjustment to keep performing well.
The standard at which your brakes operate is known as the braking efficiency; this is the maximum force capable of being developed by the brakes expressed as a percentage of the maximum gross weight of the vehicle. Measurement of braking efficiency requires specialised equipment not normally present in farm workshops but may be available from your local approved brake test provider.
Information on dealers who can carry out brake testing is available from BAGMA.
Other machinery testing includes LOLER (Lifting Operations and Lifting Equipment Regulations) testing. Read our guide on what the law says on lifting equipment to find out more.